Sheet Metal Processing for Precision Equipment
Full-service partner for sheet metal processing relies on high-end software from North Germany.
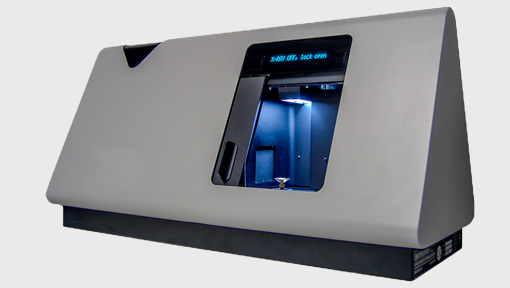
The Dutch sheet metal specialist Contour Group worked with a customer to develop the sheet metal housing for an X-ray scanner used in microtomography. The housings are now serial produced at Contour. The highest grade of accuracy and precise manufacturing are prerequisites for these devices. Within the Contour Group, the Contour Covering Technology – located in Winterswijk, the Netherlands – is the competence center for sheet metal processing. Machine frames, boxes, and housings as well as machine claddings for various customers are created here based on their individual requirements.
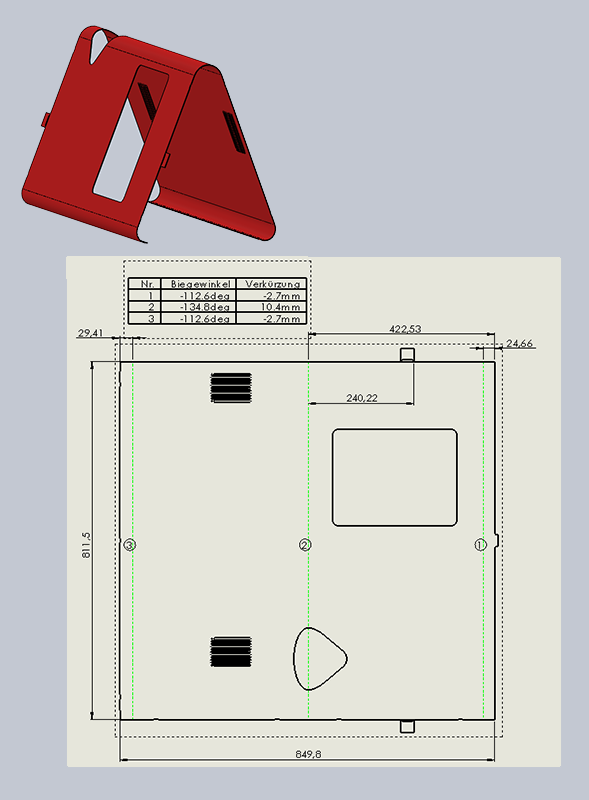
The availability and mastery of various technologies, from design software and sheet metal processing machines to high-tech assembly, is a matter of course for Contour.
X-ray microtomography equipment for research and industry
X-ray microcomputed tomography is one of the most powerful methods not only for particle analysis but also for medical diagnosis. The internal structure of examined objects can be analyzed in 3D down to the micrometer range without destroying the object. This method is an important analytical tool for material optimization and quality control of components. Such scanners are also used in medicine and pharmacy. For example, for the release of pellets and granulates, the quality of the individual layers is crucial. Micro-CT can be used to detect defects in the functional layers. For these and other tasks, the industry has developed devices that can detect such tiny problem factors or particles and map them with the help of software. Microtopography is a method with a resolution of fewer than 5 micrometers (µm). By comparison, conventional computer tomography can only detect objects that are larger than about 0.5 mm.
“As a full-service partner for our discerning customers, we want to constantly invest in the further training of our employees, in machines and systems, in IT and communication and, of course, in production automation,” emphasizes Jonas Simmes, production engineer at Contour in Winterswijk. To achieve this, the company also relies on software from the North Germany-based SPI GmbH, a software developer committed to the “digitization of the sheet metal process chain.”
An integrated process from the sketch to the detailing to the finished assembly, all in 3D: just a few years ago it was a dream of the future. Now it is standard in the design department at Contour. Even more important – in terms of the process chain – is the error-free transfer of data from CAD to manufacturing. If the machine supplier’s systems don’t play along, you have to look for other professionals.
From Design to Manufacturing
In manufacturing, Contour relies on state-of-the-art equipment from the world market leader in Ditzingen, Germany. The products created on those machines, which are then mainly used in a high-tech environment, are made mostly from sheet metal in thicknesses between 0.3 and 5 mm. Here precision is the minimum requirement. “However, when it came to feeding our high-end laser and bending machines with the calculated data, there were always problems that could not be easily solved with the machine supplier’s software,” Jonas Simmes explains.
“This unnecessarily cost us time and machine resources. We looked around for alternatives. After researching the market, we came across SPI GmbH from Ahrensburg, Germany, which defines itself as a specialist for digital processes in sheet metal processing. After the first test license in 2017, we soon decided to implement the software. Since 2018, we have been running several licenses of the Solidworks-based SheetMetalWorks software, which we have supplemented with additional licenses of the SPI Trumpf Interface.”
Consistent Data within the Process Chain
The production engineer sees the consistent usability of the underlying data as a major advantage of the software. Processing within the digital process chain takes place according to the following pattern: defining the calculation basis, considering the production-relevant parameters already during design (error exclusion principle), defining output formats, generating calculation and output, and, finally, transferring the data to downstream programs for machine control. “Thanks to SPI, the consideration of the manufacturing-relevant machine-specific parameters and the use of the real bending radii now ensures smooth execution even for complex bending sequences,” confirms Simmes.
The basis of the calculation is the data maintained in the Material and Tool Manager of the SPI software. The program generates the flat pattern and provides corresponding output formats that contain all data relevant to production. The SPI TruTops Interface is based on material and bending process information, including the bending factors and production radii, that are read from TruTrops Bend into the SPI Material Editor and are then used as a basis already during the design phase. For the programs of the TruTops family, SPI software generates all relevant manufacturing data in the TruTops GEO format or in the extended DXF format (including opening angle, radius, bending tool combination, and bending technology). In addition, SPI supplies a manufacturing-ready STEP file with the specific process information for bending with TruTops Boost.
1:1 into Production
“As a rule, the data is correct straight away and we can pass it on to production 1:1,” summarizes production engineer Simmes. “The acquisition of the software paid off quickly. Thanks to the good order situation, we can invest the time gained in new projects.” The Contour Group has once again taken a step towards the goal of optimally supporting its customers thanks to its own expertise, state-of-the-art tools, and competent software solutions.
The Conclusion
What was the challenge?
When it came to feeding our high-end laser and bending machines with the calculated data, there were always problems that could not be easily solved with the machine supplier’s software.
What have you gained?
Thanks to SPI, the consideration of the manufacturing-relevant machine-specific parameters and the use of the real bending radii now ensures smooth execution even for complex bending sequences.
In a nutshell: the main advantage?
The acquisition of the software paid off quickly. Thanks to the good order situation, we can invest the time gained in new projects.
What would you like others to know?
In terms of the process chain, an error-free transfer of data from CAD to manufacturing is crucial. If the machine supplier’s systems don’t play along, you have to look for other professionals.
Reference as PDF
Here you can download the story, including all images.
Our Products
We help you to streamline your sheet metal process chain.
Our Offer
You would like to try it yourself? Contact us!
And More
Here you can find more references and stories.